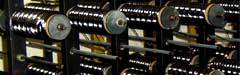
Production process
Carbon or glass fibers are conveyed through a rack from the
bobbins to the resin tank for the impregnating process.
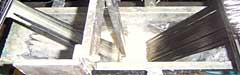
The impregnate fibers are conveyed through a warmed mould
for the polymerization process under pressure; by this
operation the empty spaces between the fibers are removed.
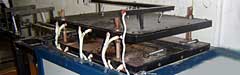
Usually the mould is warmed with resistors controlled by
thermocouples. The warming time depends of the production
speed.
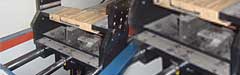
During the moulding and the polymerization process the
profile is moved out by the pulling system at fixed speed
and it’s cut at the needed length by a disk saw.
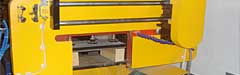
During the production process the profile can be reinforced
outside and inside along various axial directions by fitting
in some strips of mat or carbon fabric, or by winding it
with carbon filaments |

|
Composite
Materials
Composite
materials are made with fibers as glass, carbon,boron and aramidic
fiber, included in a resin matrix (polyester, vinil, epoxy, phenolic)
which does not have tasks of meccanical resistance, but guarantees
the cohesion between the adjacent layers. Their discovery is due to
the large engagement, as well economic as human, of the aerospace
industry in tecnological search.
Really in the a.m
field this industry spent many efforts to obtain the better
compromise between resistance, weight and cost for the structure of
the aircraft and to realize the best performance in terms of
energetic saving.
As regards this
matter, the metallic materials have not totally satisfied the
conditions previously exposed, due specially to the high costs and
the difficult in assembling the strutture; therefore the researchers,
at the beginning of the years sixty, tried new solutions.
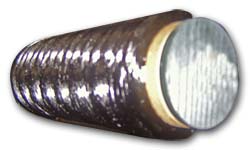
The greater
attentions have been turned towards those elements that introduced
bottom values of molecular weight as the lithium, beryllium, boron
and carbon. It discards the lithium and the beryllium which are more
espansive and not easy to find, the searches have concentrated on
boron and carbon.
With fibers made
up of carbon, they have been resolved also some economical
disadvantages thanks to a better technology of production and the
greatest availability of this element in nature. As departure
products have been chosen poliacrilonitrile and the rayon, two
polymers which have a strong percentage of carbon (beyond 65%) and
adapted characteristics for being able to face the tranformation
process.
In order to reach
the production of fibers, in fact, the polymers must endure before
the pyrolysis (variation of the chemical compositions for effect of
the heat) to aproximately 200 °C in oxygen presence and the
elimination of the elements different than the carbon.
The highest
meccanical characteristics are due to a traction exercised on the
fibers during the a.m. two process and can partially be modified by
changing the temperatures. In the year 1971 an other product, the
aramidic fiber, joined the carbon as material having advanced
meccanical an peculiar characteristics, leaving not from syntetuc
polymers but from an organic compound, the aromatic poliamyde, for
which the production process still protected from world-wide licence. |